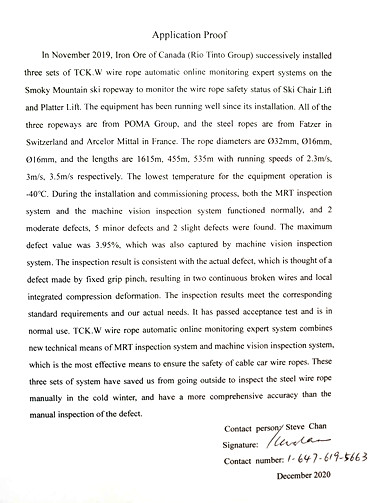
Weltweit führend in der zerstörungsfreien Prüfung von Drahtseilen
Spotlight Technology Innovation Award
Rede zum OTC Award: TCK.W Das automatische Online-Erkennungssystem für Drahtseile wird die Art und Weise der manuellen visuellen Inspektion auf regelmäßiger Basis völlig verändern. Durch die kontinuierliche und ununterbrochene Erkennung während des Betriebs des Drahtseils wird es die Sicherheitsüberwachung des Drahtseils verbessern Drahtseil auf den höchsten Stand.
Gewann die höchste Auszeichnung im National Disruptive Technology Innovation Competition 2022 des Ministeriums für Wissenschaft und Technologie
Ministerium für Wissenschaft und Technologie: Disruptive Technologien sind innovative Technologien, die „die Spielregeln ändern können“. Es wird die ursprüngliche Technologie übertreffen und Substitutionen hervorbringen, was den transformativen Effekt haben wird, dass eine neue Möglichkeit geschaffen wird, die Entwicklungskurve der Technologieentwicklung zu ändern und die aktuelle Situation zu untergraben.
Luoyang Wire Rope Inspection Technology Co., Ltd. (kurz TCK.W) ist ein nationales Double-High- und Double-Soft-Unternehmen, das sich auf die Erforschung der zerstörungsfreien Prüftechnologie für ferromagnetische Materialien spezialisiert hat, und ein spezialisiertes und besonderes neues Unternehmen in der Provinz Henan.
Magnetic Memory AI schwach magnetische zerstörungsfreie Prüftechnologie“ ist die erfolgreiche Entdeckung der sich ändernden Bewegungsregeln des mikroskopischen Materials „magnetische Domänen“ und „elektronenspinmagnetisches Moment“, die durch den Quanten-Vielteilcheneffekt in gebildet werden, durch TCK.W-Wissenschaftler Die wichtigsten wissenschaftlichen und technologischen Errungenschaften auf dem Gebiet der zerstörungsfreien Prüfung sind auf internationaler Ebene führend (laut Angaben des Ministeriums für Industrie und Informationstechnologie), und die Technologie hat sechs große Innovationen und zwei große Durchbrüche erzielt.
1. Theoretische Innovation: Erstellen Sie ein neues Prinzip der „Raummagnetfeld-Vektorsynthese“
2. Methodeninnovation: Entdecken Sie eine neue Methode der „magnetischen Gedächtnisplanung“ (Erfindungspatent)
3. Technologische Innovation: Erfindung der neuen Technologie „schwacher Magnetsensor“ (Erfindungspatent)
4. Materialinnovation: Erfindung eines neuen dünnen Streifenmaterials aus einer amorphen weichmagnetischen Legierung (Erfindungspatent)
5. Algorithmusinnovation: zerstörungsfreie Bewertungsmethode der Drahtseillastleistung (Erfindungspatent)
6. Produktinnovation: Erfindung einer Reihe schwachmagnetischer Erkennungsprodukte für Drahtseile (Erfindungspatent)
Durchbruch 1: Durchbruch von der qualitativen Erkennung zur quantitativen Erkennung; Durchbruch 2: Maschinelle intelligente Erkennung ersetzt manuelle Erkennun
Nationaler Erfindungspreis
Wissenschaftlicher und technologischer Fortschrittspreis der Volksbefreiungsarmee
Technologie-Innovationspreis des Ministeriums für Wissenschaft und Technologie
Die höchste Auszeichnung des Ministeriums für Wissenschaft und Technologie
● Hebetechnik, Stahlkernförderbänder, Wasserschutztechnik und andere Branchenlösungen – klicken Sie bitte auf den Pfeil unten●
Durch die integrierte Anwendung von industriellem Internet + magnetischer Speicher-KI-Technologie zur schwachen magnetischen Erkennung + maschineller Bilderkennung und intelligenter Überwachungstechnologie in der Sicherheitsproduktion kann die TCK.W-Technologie die Wahrnehmung, Überwachung, Frühwarnung, Entsorgung und Bewertung des sicheren Betriebs des Kabels verbessern Seil während seines gesamten Lebenszyklus, realisieren den Wandel der Drahtseilsicherheit von der statischen Analyse zur dynamischen Wahrnehmung, von der Nachsorge zur Vorbeugung, von der manuellen Erkennung zur intelligenten Überwachung und verbessern das intrinsische Sicherheitsniveau des Drahtseilbetriebs. Es hat für die Nutzer einen enormen Mehrwert im Hinblick auf Energieeinsparung und Emissionsreduzierung, Kostensenkung und Effizienzsteigerung, Maschinenaustausch und das Erreichen der doppelten Kohlenstoffziele geschaffen.
Bergbauindustrie-Anwendung vor Ort
Hafenindustrie-Anwendung vor Ort
Öl Industrie-Anwendung vor Ort
●Seilbahn, Aufzug, Förderband vor Ort, bitte klicken Sie auf den Pfeil unten ●